The Ripple Effect
-News and Commentary-
A Future Built by Hands That Aren’t Ours
- Home
- News and Commentary
- A Future Built by Hands That Aren’t Ours
Share On Social
Today in The Ripple Effect, we are discussing a quiet shift that just got real loud. Last week, news broke out of California that a group of humanoid robots—yes, actual robots—are now working side by side with humans on the assembly lines of an auto shop. These aren’t science fair prototypes or PR stunts. These are full-scale, functioning mechanical workers, designed by a company called Figure, now standing shoulder to shoulder with real people, building real things, on real factory floors.
And yet, there wasn’t a national headline in sight. No panic. No protests. Not even a prime-time debate. Because unlike most major tech moments, this one doesn’t feel like a boom—it feels like a shift. A quiet click. Like when the gears of history start turning again and you realize: Oh… we’re not going back.
California wasn’t the first. It just made it real. Back in January 2024, BMW quietly announced a partnership with Figure to bring these humanoid machines into their production environment. The test site? Their plant in Spartanburg, South Carolina. The model? Figure 02—a 5-foot-6, 150-pound robot with two legs, two arms, and a brain powered by next-gen AI.
It doesn’t just look like us—it moves like us. Think: human-scale hands with 16 degrees of freedom per hand. Cameras, mics, sensors, and a nervous system of processors running three times faster than its predecessor. This robot can see, hear, and react. It can insert sheet metal into car chassis, work in tandem with humans, and adjust to real-time variables on the floor. It’s not just advanced. It’s autonomous.
But this isn’t a takeover story. It’s a growth story. Let’s pause here—because usually when robots come up, so does panic. The headlines scream automation, layoffs, AI stealing jobs, and dystopian futures. But that’s not where this episode is going. This isn’t a story about machines replacing people. This is a story about people evolving alongside machines.
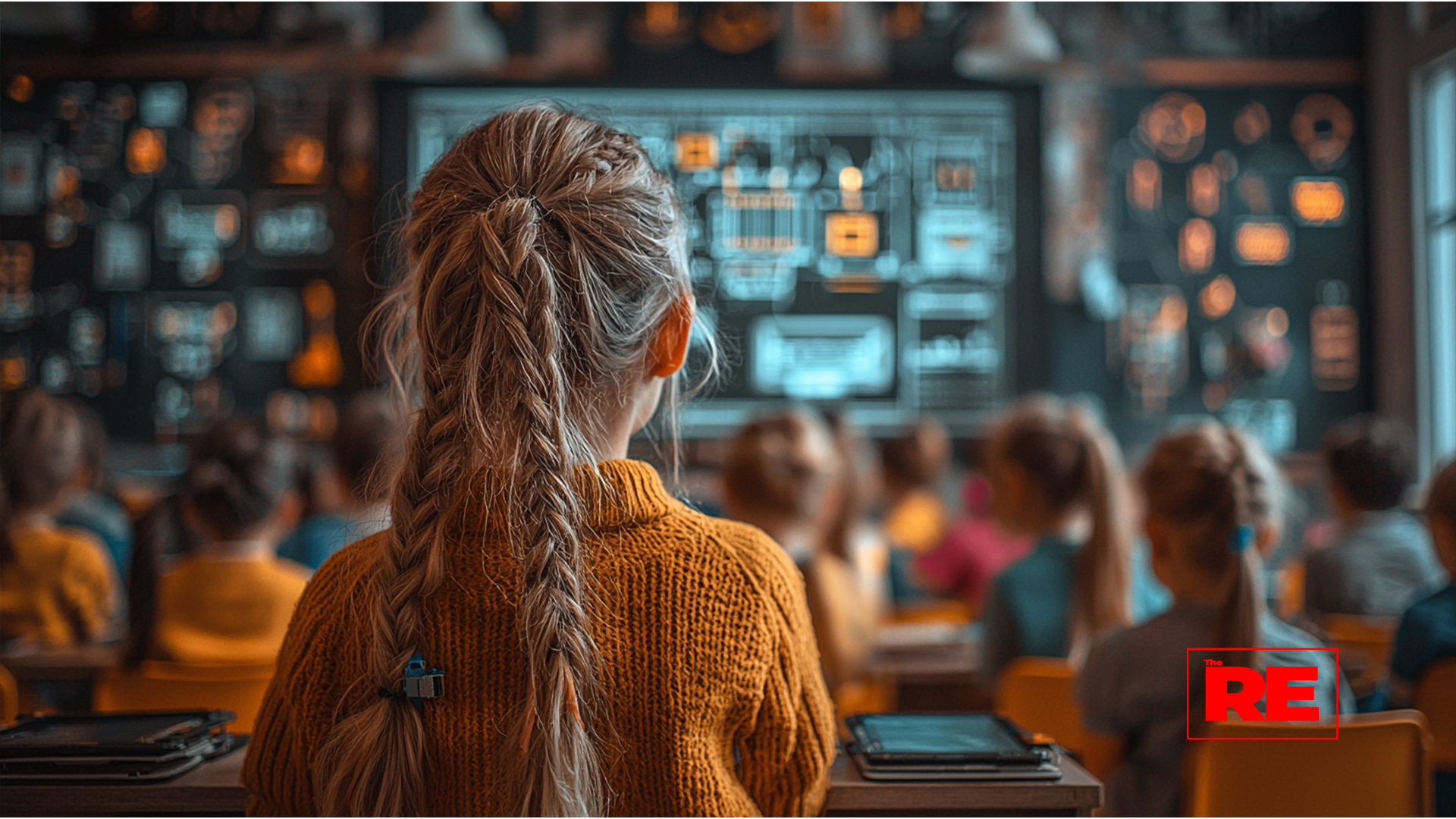
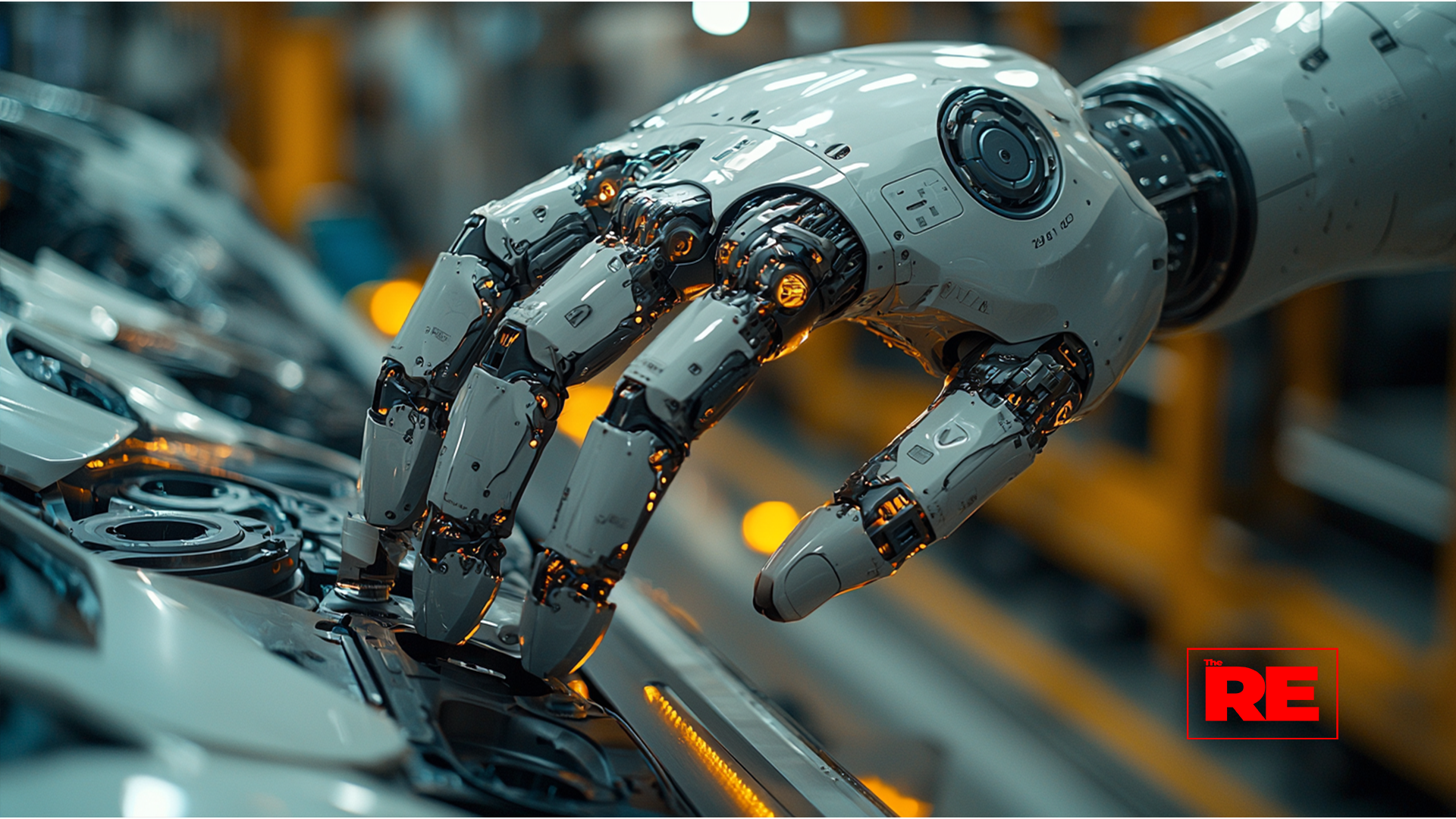
Because what’s happening in California—and before that, in South Carolina—isn’t the collapse of labor. It’s the next phase of work. And yeah, it’s different. But it’s not inherently destructive. If we do it right, it might be one of the most liberating shifts in human labor we’ve ever seen.
Think about it: why do we work? Why do we spend the best hours of our days doing tasks that are physically taxing, mentally draining, or straight-up dangerous? Because for the last hundred years, we’ve had to. Work was survival. We didn’t have a choice.
But what if the future of work isn’t about survival—it’s about service? What if, instead of humans bending over assembly lines, we trained machines to do that heavy lifting—literally—and we reoriented human labor toward innovation, community, care, and creation?
That’s not a fantasy. That’s where this is heading.
Let’s be real: Figure’s robot isn’t building Teslas in a solo act. It’s not making decisions, filing taxes, or raising kids. It’s bolted into a very specific lane—tasks that are unsafe, repetitive, or ergonomically damaging. In the BMW tests, the Figure 02 inserted sheet metal into a fixture—a job that requires high precision, but not high creativity.
And that’s the key. These humanoid robots aren’t here to take over your mind. They’re here to take over the tasks you shouldn’t be forced to do in the first place. Tasks that wear out joints, break backs, or dull ambition over time.
So no, this isn’t about job loss. It’s about job evolution. And for that to happen, we have to reshape what “valuable work” means in this country.
If humanoid robots are going to handle the grinding, high-repetition tasks on the floor, then the humans around them have to level up. That’s not optional. That’s survival. And that’s where education becomes the frontline.
We need to stop thinking of education as a pipeline to fill jobs—and start treating it like the foundation to redefine them. That means universal access to STEM, sure. But more than that, it means teaching problem-solving, critical thinking, ethics, and human creativity—because those are the things machines can’t replicate.
In this world, we need people who can operate, repair, and optimize these machines. People who can write the code that drives their logic. People who can set safety standards and ethical guardrails. People who can use freed-up time to solve real-world problems beyond the factory.
We also need leaders who can reimagine what a workforce even looks like when “work” stops being a matter of survival, and starts being a matter of contribution.
That’s why this Figure partnership matters. BMW didn’t just roll out robots and call it a day. They rolled them out in a controlled, intentional way—placing them in roles that complement human workers, not compete with them. They’re automating tasks that slow down production—not the people who bring it to life.
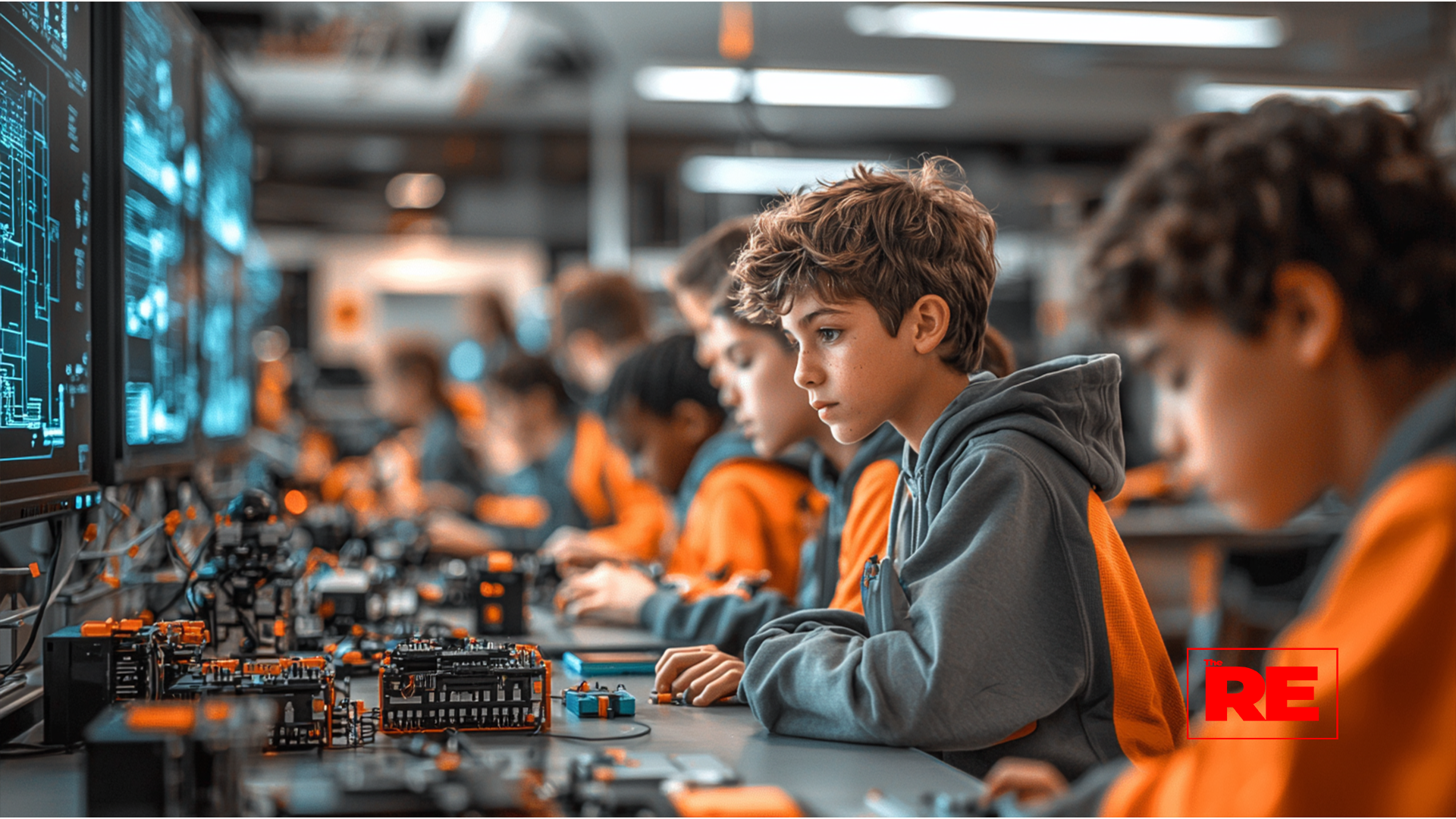
And that’s the blueprint. Robots should be treated like tools, not threats. Assets that support the workforce, not replace it. And if businesses are smart, they’ll realize something else too: the better trained your humans are, the more effective your machines become.
We’ve had revolutions before. The industrial kind. The digital kind. And yeah, they always come with some pain. But what makes this moment different is that we’re walking into it with foresight. We can see the direction. We know what’s coming. We have a choice.
This isn’t about fighting off automation with picket signs. It’s about demanding that automation works for us—not around us. And maybe, just maybe, it’s about redefining labor itself. Because if machines can build the cars, maybe humans can finally build the future.
If the first wave of robots hit the manufacturing floor like a warning shot, this next wave—humanoid, AI-enhanced, adaptable—is coming like a shift in the tide. And here’s the thing about tides: they don’t ask permission. They don’t wait until everyone’s ready. They rise.
So the question isn’t “Will robots take over?” It’s “Will we be ready for what they leave behind?”
Let’s talk readiness. Let’s talk education.
What we’re seeing unfold in California isn’t just a tech demo—it’s a mirror. It’s showing us what happens when progress moves faster than policy, faster than school curriculums, faster than public awareness.
These humanoid robots—like the Figure 02—aren’t here for fun. They’re being brought in because they can work longer, lift heavier, and follow precision tasks without fatigue. That’s not evil. That’s efficiency. And in a business sense, it makes total sense.
But what does it say about our system if we’re still preparing students for jobs that won’t exist by the time they graduate?
That’s the wake-up call. If we don’t start adapting how we teach, not just what we teach, we’re going to end up with a population that’s overqualified for the past and underprepared for the future.
We’re talking about STEM programs in elementary, not just high school. Coding, robotics, and systems thinking taught alongside reading and writing. Trade schools that train for automation management, not just legacy machines. Community colleges that pivot from diploma mills to innovation hubs.
Because if the robots are taking the wrenches, we need to hand humans the blueprints.
This isn’t just about training individuals. It’s about building systems that can keep up with the speed of change. Think about what a robot-filled auto shop actually needs: high-speed connectivity, advanced cybersecurity, specialized technicians, energy-efficient power grids, and ethical oversight bodies.
That means government can’t sit on the sidelines anymore. If we’re going to create a world where humans and machines work together, we need real investment in the infrastructure that supports that.
It’s not enough to say, “Learn to code.” You can’t code your way out of a system that doesn’t give you the tools, funding, or access to participate in the first place.
Let’s keep it real—businesses are moving faster than governments. Always have. But this tech boom we’re in now? It’s moving lightyears ahead of legislation. And if policymakers don’t catch up, they’re not just falling behind—they’re putting people at risk.
Because where there’s innovation, there must be protection.
We need federal standards for human-robot interaction in the workplace. Labor laws that redefine what it means to be “on the job.” Education reform that aligns with real-world demand. Data privacy protections for environments powered by AI. And maybe most of all… a national narrative that this isn’t scary. It’s necessary.
When we see robots walking factory floors, our first instinct shouldn’t be fear. It should be vision.
Now let’s hit something nobody really wants to touch: if robots are doing more of the labor… do humans still need to work? Short answer? Yes. But the long answer is more interesting. Because maybe we’ve been asking the wrong question. Maybe it’s not “What jobs will be left?” Maybe it’s: “What kind of society do we want to build with the time we gain back?”
If a robot can assemble a car, clean a warehouse, or prep an order—what does that free us to do?
We could focus more on education, arts, and caregiving. Invest in climate solutions, health innovation, or mental health services. Strengthen local economies through micro-enterprise and entrepreneurship. Volunteer more, parent more, create more, rest more.
But that future only works if we stop tying human worth to work output. We have to stop seeing labor as identity and start seeing it as opportunity. When effort isn’t required for survival, it becomes a choice. A contribution.
Figure’s humanoid robots aren’t a gimmick. They’re a glimpse. A glimpse of a world where technology supports humanity—not replaces it. A world where physical labor becomes optional. Where mental effort is redirected. Where human creativity, care, and consciousness are elevated above the grind.
But that only happens if we build a bridge between now and next—with policy, education, and real leadership. Because if we ignore it, we don’t get a utopia. We get chaos.
Every major leap in history—the plow, the steam engine, the internet—disrupted the way people lived and worked. But it also opened doors we didn’t know existed. This moment is no different.
The robots are here. They’re not marching in. They’re walking in—on two legs, built by us, powered by us, working for us… if we let them.
So the real question isn’t whether they’ll change the world. The real question is: will we change with them—or get left behind trying to defend a world that’s already gone?
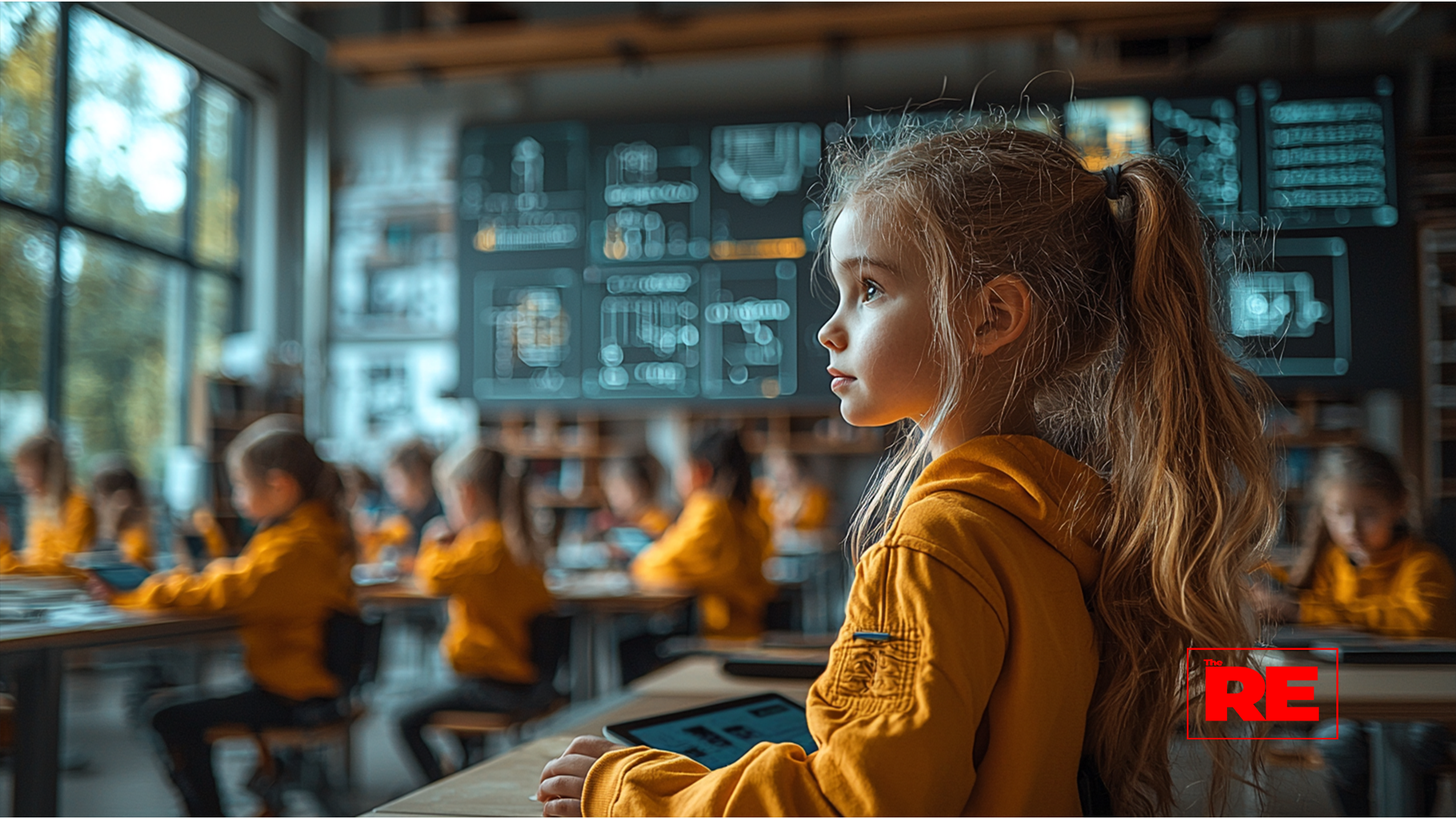
"Truth survives because of you. Make your gift count."
Every dollar helps us fight misinformation and dig deeper into stories that matter.